NO LONGER AVAILABLE.
REF# 188538
Equipped as follows:
CONVERTIBLE STOCK:
Paper (depending on quality), min. 70 g/m2
Board (depending on quality), up to (*) 2000 g/m2
Corrugated board, (micro-flute) up to ( • ) 2.0 mm
( * ) Carton acceptable warp: 4% of the widthwise sheet
SIZES
Sheet size, max. 1060 x 760 mm
Sheet size, min. 400 x 350 mm
Stamping and embossing size, max. 1050 x 742 mm
DIMENSION OF PALLETS:
Feeder/ delivery, max. 1200 x 800 mm
PRODUCTION
Force developed, max. 100% FTU (Foil Touch Units)
Production rate for stamping: (depending on foil advance and width), up
to 8000 sheets / hour
PILE HEIGHT
Feeder: normal mode, max. 1400 mm
Feeder: Non-Stop mode, max.1100 mm
Delivery : max. 1160 mm
Delivery : Non-Stop mode, max. 1160 mm
PILE HEIGHT- ELEVATED MACHINE
Elevation I: 420 mm
Feeder: normal mode, max. 1820 mm
Feeder: Non-Stop mode, max. 1520 mm
Delivery : normal mode, max. 1580 mm
Delivery: Non-Stop mode, max. 1580 mm
Developed and optimized for the Hot Foil Stamping process, and maximal ergonomic, including:
– Concepts “Space+” and “Keyless” for new levels of user friendliness.
– Platform OS and OOS.
– Cam driven technology for HFS with “Foil Touch System”. Power Register II and Smart Feeder Foil.
– Magnesium and carbon fiber gripper bars technology, with bottom grippers.
– Dynamic air blast system at platen outlet permitting sheet stabilization before impression then foil release.
– Dynamic gripper bars chain’s tension system for longevity and ideal sheet conveyance.
– Multiple automated functions such as machine programmed stop for quick job changeover or delayed stop if miss registered sheet (permitting
delivery of sheets in process).
Centerline system for quick job changeover. Electronic device for sheet travel control.
Control cabinet cooling unit.
Bobst-Electronic machine operating system CUBE3 (Control Unit Bobst Electronic) with color touch screen.
System controlled by a designed by Bobst microprocessor, allows operator to easily control, visualize
and check the various functions and elements of the machine.
2 Units (15″ screens) are included as base equipment for optimal ergonomics
Main motor with frequency converter control.
The Smart Feeder includes:
– Independent feeder with electrical drive-shaft.
– Automatic lateral pile tray correction (+/- 40 mm) controlled by the Power Register II.
– Full automatic synchronizing device for sheet arrival controlled by the Power Register II.
– Automatic height adjustment of suction unit.
– Motorized adjustment of transport suckers.
– Additions to the suction unit with individual height adjustment of external forwarding suction cups.
Manual non-stop device.
Photocells for automatic cycle at the feeder.
Continuous pile raising whilst maintaining a constant height for the top of the pile. Side blowers adjustable.
Suction unit with multiple adjustments.
FEED TABLE:
POWER REGISTER II
Device ensuring registering without sheet edge contact : either in relation to the sheet edge or the printing.
Covered with an anti-static stainless steel plate. Feed table inlet equipped with lateral ramps.
Double sheet detection with automatic calibration controlled by the POWER REGISTER II. Upper frame with pneumatic lifting device.
Upper transport equipment for paper and paperboard. Transport belts.
With lateral guidance and automatic tensioning system.
PLATEN
Foil Touch System (FTS)
New concept of optimization using cam driven mechanism for hot foil stamping process, involving the time under pressure, the strength applied and the operating temperature.
Short stroke movable platen, driven by a cam mechanism.
Controlled cam movement allowing smooth acceleration and deceleration during the sheet transfer process.
Matched Rigidity concept applied to the platen design granting a perfect gap regardless of the pressure.
Heated upper head.
With 12 independent heating zones.
Automatic “on and off” pressure device of the platen. Equipment centering and locking.
Automatic equipment centering and locking for chase and supporting plate. Micrometric centering for stamping plate (+I- 0.9 mm).
Measurement of the stamping force with strain gauge. Motorized stamping force setting.
Steel stamping supporting plate.
Thickness 12 mm (0.47’1)
DELIVERY:
Pneumatically controlled front and side joggers. Adjustable rear and side joggers with Centerline marks.
Continuous lowering of the pile for a constant and minimum fall height of the sheet on the pile.
Braking Brush.
Motorized, pressure and timing of the brush are adjusted on the CUBE3. The brush action is automatic and is slated to the machine speed.
The brush and tablet are adjusted together or separately by independent motors according to the sheet length.
Automatic variable height non-stop apron. Sheet away from grippers control by photocell
HOT FOIL STAMPING EQUIPMENT:
Easy Foil System (EFS)
System permitting proper location of foil webs from the Unwinding Module:
-Assures precise foil web’s positioning in regard of the layout.
– Ergonomic, grants time savings at each job change over.
Includes an automatic foil web’s introduction system, and lateral exhaust
00S for the used foil.
Foil web transport equipment inside the machine consisting of:
– 1 cross bars device for foil web guidance,
– 71 combined blowing unit permitting to flatten the sheet before impression, then to release the foil after stamping, adjustable from the CUBE control unit.
Independent electrical cabinet BM for stamping functions.
Air conditioned electrical cabinet, permitting to control up to 6 independent advance shafts.
TOOLING:
Hot foil stamping equipment, including:
– Honeycomb chase (T-135.001)
– Stamping plate, “BM” concept (T-140.001)
– Compensating plate, “BM” concept (T-140.002)
– Graduated rule (T-130.001)
Automatic non-stop rack with lateral shifting
Stream aligner: System permitting realignment of skewed stream on feed table before registration, in full automatic mode
Load pressing device: Automatic system with timed pushers aligning sheets front edge of the top of the pile before release onto feed table.
Complement for reading 1 mm register marks Allows reading printed marks 1mm wide (2mm standard) with the Foil Register system.
Platen set point adjustment with “APC” technology System permitting automatic maintain and regulation of defined platen set point
Increase of time under pressure with “Soft Dwell” technology
Time under pressure is increase by more than 40%
Special sheet push-down blowing device at delivery
Controlled by the CUBE3, assures perfect sheet’s piling, especially when operating with light materials or paper. Includes 5 rows of 4 fans adjustable in air strength and to the sheet size.
Assures higher productivity and pile quality at high speed, especially when processing light materials (or recycle).
1 Foil Supply Module Plus with 2 advance shafts
Module consisting of:
– 2 advance shafts, each driven by 2 individual electronically
controlled motors, located on the press HFS section
– 2 festoon units driven by multiple electronically
controlled motors, located inside the module
-12 pressing rollers for advance shaft, 20mm
To operate with 6 foil webs with 3″ hubs:
– 6 electronically controlled reel holder
– 6 sets of reel holders with 3″ hub
– 1 complement for reel holder supports, heavy
Maximum 12 electronically controlled reel holder can be installed
Plate positioning rules: Recommended for jobs containing multiple and identical dies, with precise manufacturing dimensions.
Eccentric fasteners for the dies
Foil break control system for 8 foils
For Foil Supply Module Plus, consists of 8 laterally adjustable photocells.
Stops the machine immediately in case of a foil breakage.
Reel holder 3″ electronically controlled (MD+) for Foil Supply Module Plus
6 units are provided
Reel holder 1″ non-electronically controlled (MD+) for Foil Supply Module Plus
Reel holder with 3″ hub (MD+)
Includes accessories for narrow webs (without flanges)
Set of flanges D-400mm for reel holder with 3″ hub (MD+)
Removable reel holder for extra wide reels (1″)
2 units are provided with the standard equipment. Set of flanges and brake for removable reel holder (1″) Flanges D-250mm
6 units are provided with the standard equipment
Pressing roller for advance shaft (MD+)
For Foil Supply Module Plus, 20mm wide
Computer supervision system OACS – Machine Optimizes calculation of foil advances automatically for maximal foil savings and data can be stored with the Machine Supervision System (MSS).
Increases to 15 the number of foil advances combinations
VacuFoil System: Operative evacuation device for used foil webs to be connected to an in-plant existing suction system with shredder (to be provided by customer). In-plant suction system must be connected and operational at starting of machine’s instruction program.
Control table
Table for optimal control of a stamped sheet at delivery.
Fixed on the platform, includes a lighting system with automatic start-up.
Presetting table for the die mounting plates
QUALITY CONTROL & RELATED SYSTEMS:
Additional “CUBE” control panel Unit
MSS Console (Machine Supervision System)
Interface permitting installation of softwares to enhance connectivity and/or productivity. Permitting specific programming, storage of job’s settings, the use of the maintenance program and its automatic follow-up, and installation for the Service software’s (optional). Import and export of job’s settings via the USB key.
MSS is installed on the pivoting CUBE unit located at the delivery
station (pivoting) or on the Control Table (0-100.001). Including a USB port.
Interface enabling the connection of a unit for waste treatment. This interface accounts for our equipment’s and processes specifics needs. Recommended when installing a shredder and/or compactor
Honeycomb chase: Including fastening set for embossing dies. Height of embossing dies 7 mm
Die mounting plate saver chase
Stamping plate, “BM” concept
Thickness 2.3 mm
To be used with compensating T-140.002
Stamping/embossing die mounting plate including mounting screws
Height of embossing dies, 7 mm (0.3′)
This plate is specific to MASTERFO/L 106 PR
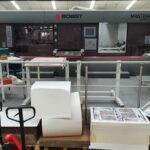